
Data Centers rely on uninterrupted power supply,
Backup generators fueled by High-Speed Diesel (HSD) play a key role, Fuel polishing units purify stored HSD to prevent contamination, Clean fuel is vital for Data Centers’ smooth operation.
The Need:
In today’s online world, data storing has become an important aspect, hence we are seeing a meteoric rise in the number of Data Centers that have being constructed across the world.
These Data Centers or Data Houses stores most critical data around the planet which facilitates operations for most of the industries today. Hence it has become a necessity to ensure that these Data Centers are always online.
This is made possible by having Backup Generators which provide power in the event of a power failure. These backup generators require High Speed Diesel or HSD for their operation, which is generally stored in large tanks and fed to them on demand.
Fortunately, today the amount of power cut experienced by the industrial sector is almost zero. But the Data Centers must always be prepared to prevent power failure and have enough fuel for operation in case of power failures for days, as even a power failure of few seconds can cause huge financial losses.
To achieve this, large amounts of HSD are stored in number of bulk storage tanks. This HSD can get contaminated over a period of time if not consumed, this contamination usually consists of the following:
- Water contamination
- Microbial contamination
- Particle contamination
This can also be passed on from the source of the HSD which are usually transported using road tankers.
These contaminants if passed on to the generators may cause damage to the equipment hence causing break downs in these critically important backup generators.
Hence it becomes a necessity to ensure that that the HSD in the storage tanks is free from contaminants. This is achieved by ‘polishing’ the fuel using what we call Fuel polishing units.
The process:
A Fuel polishing system for data center is designed in accordance with the N+1 redundancy concept. This is achieved as depicted below:
Fuel Polishing Unit – 1 Set
As shown in the figure 1 Fuel Polishing Unit consists of 1W + 1S system.
Process:-
Fuel polishing is the technical cleaning process which removes water and particulates from fuel stored for the medium to long term. This process keeps fuel at optimum condition and helps prevent fuel related engine and generator failures.
- The fuel will be pumped through predefined stages at a very high pressure to remove the water, sludge, microbial contamination and other contaminates from the fuel. This system assures you to maintain the Fuel Quality of ISO 4406 by using compatible filter elements.
- This unit uses a progressive filtration and conditioning regime:
- Coarse straining through 100 microns.
- Pre-filtration through 25 microns’ cleanable metal filter
- Final filtration through 1 microns’ disposable media filter
- Water coalescing up to 10 PPM.
- Water separation and collection
The time for operation to complete depends on the following:
- Amount of fuel to be polished
- Flow rate of selected Fuel polisher
- Pipeline size
- Filter health
To ensure that the system correctly runs the fuel polishing system provides the following:
- Filter choked status
- Emergency Stop
- Auto water drain
- PLC-HMI for monitoring & control of the system
- BMS connectivity through Modbus RS-485 RTU or Modbus TCP/IP.
- Warless connectivity through GSM based communication.
Apart from the above we also offer the following optional features:
- Viscosity Measurement
- Density Measurement
- Particulate detection (in ISO code)
- Water or Moisture contamination (in saturation RH%)
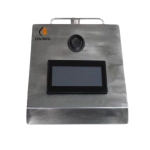
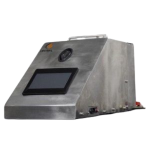



